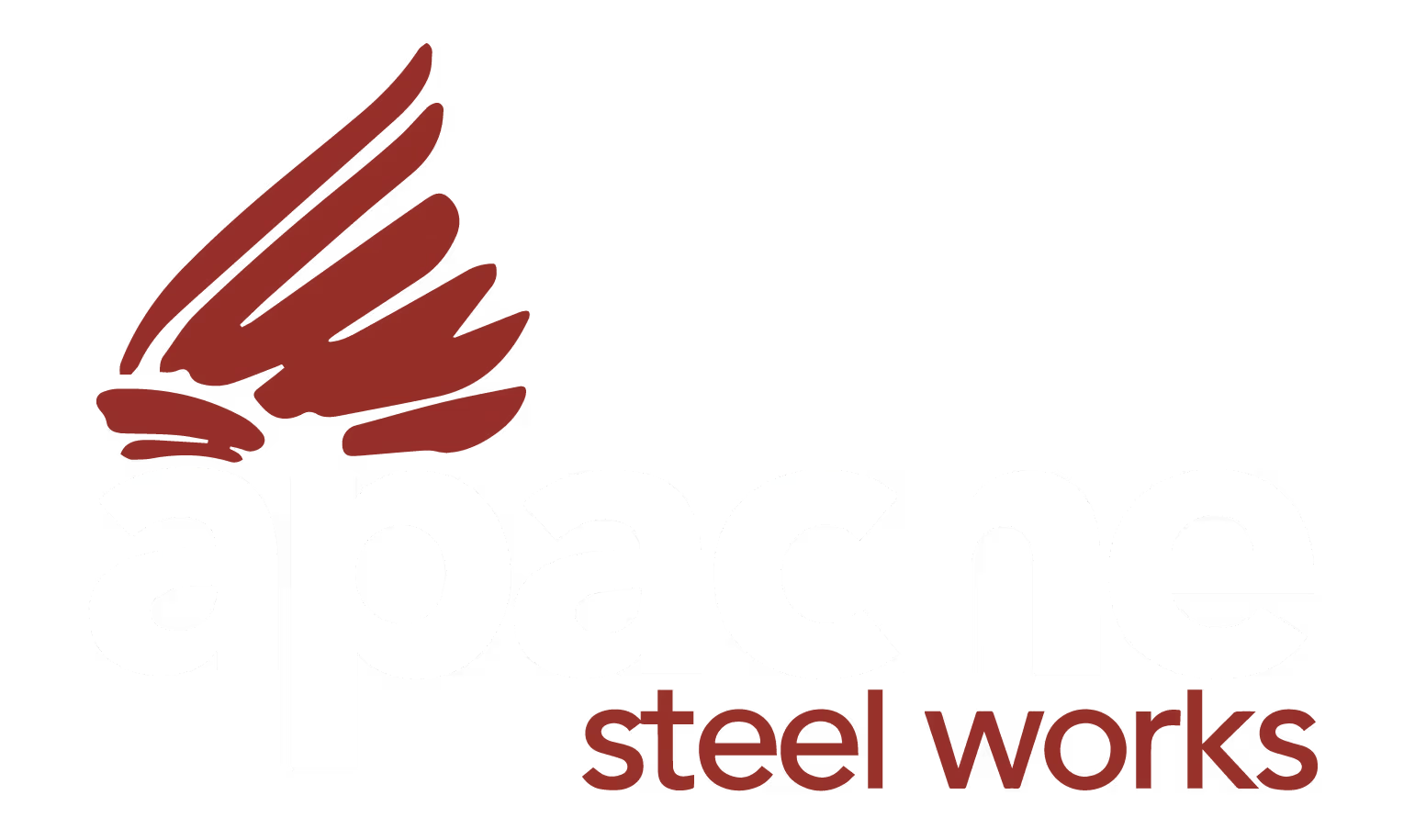
Plate Processing Company
Which Materials Are Used in Industrial Flame Cutting?
Which Materials Are Used in Industrial Flame Cutting?
The process of industrial flame cutting in Houston stands as a cornerstone of modern manufacturing, transforming raw materials into precisely shaped components. This thermal cutting technique relies on controlled chemical reactions between oxygen and metal, creating clean, accurate cuts through various materials. Understanding the materials involved in this process helps optimize cutting performance and achieve superior results.

The Science Behind Industrial Flame Cutting
Industrial flame cutting in Houston operates on a fascinating principle where preheated metal reacts with pure oxygen to create a controlled oxidation process. This reaction generates intense heat, reaching temperatures up to 3,000 degrees Celsius, which effectively melts and removes material along the cutting path. The preheat flames, typically fueled by acetylene or propane, warm the metal to its ignition temperature before the cutting oxygen stream initiates the actual cutting process.
Materials That Work Best with Flame Cutting
Carbon steel emerges as the primary material choice for industrial flame cutting in Houston, particularly due to its excellent oxidation properties. The carbon content in steel creates an ideal environment for the flame cutting process, allowing for clean, efficient cuts across varying thicknesses. Low to medium carbon steels respond exceptionally well to flame cutting, producing smooth cut edges with minimal post-processing requirements.
Another material that can be efficiently cut using flame cutting is wrought iron because this material has favorable thermal properties and low carbon content.
Cast iron presents unique challenges in flame cutting operations. The high carbon content and presence of silicon in cast iron can affect the cutting process, often requiring specific adjustments to cutting parameters. Despite these challenges, skilled operators achieve successful results by maintaining precise control over preheating temperatures and oxygen flow rates.
Critical Factors in Material Processing
Material thickness plays a crucial role in determining cutting parameters. Thicker materials require longer preheating times and adjusted cutting speeds to ensure complete penetration and clean cut edges. The composition of materials directly influences their behavior during cutting, with elements like chromium and nickel affecting the oxidation process.
Cutting speed varies depending on material properties and thickness. Proper speed selection ensures optimal cut quality while preventing issues like excessive dross formation or incomplete penetration. The relationship between cutting speed and material thickness follows a non-linear pattern, requiring experienced operators to make appropriate adjustments.
The selection of fuel gas significantly impacts cutting performance. While acetylene provides the highest flame temperature, alternative gases like propane offer economic advantages in certain applications. Oxygen purity levels directly affect cut quality, with higher purity oxygen typically producing cleaner cuts and faster cutting speeds.
Industrial Applications and Material Considerations
The shipbuilding industry extensively utilizes industrial flame cutting in Houston for processing thick steel plates. The ability to cut through substantial material thicknesses while maintaining acceptable tolerances makes flame cutting indispensable in marine construction. Specialized cutting techniques accommodate the unique requirements of marine-grade steels and complex geometries.
Heavy equipment manufacturing relies on flame cutting for processing large steel components. The versatility of the process allows for cutting various material grades and thicknesses commonly used in construction equipment. The ability to handle irregular shapes and varying material thicknesses provides manufacturers with essential flexibility in their operations.
Metal fabrication operations depend heavily on flame cutting capabilities. The process accommodates the wide range of steel grades and specifications used in structural applications. The combination of speed and accuracy makes flame cutting particularly valuable in high-volume production environments.
Conclusion
The selection of appropriate materials significantly influences the success of industrial flame cutting in Houston. Understanding material properties and their interaction with the cutting process enables optimal results across various applications. Carbon steel and wrought iron remain the most commonly processed materials. The continued reliability and effectiveness of this cutting method ensure its position as a fundamental manufacturing process across numerous industries.