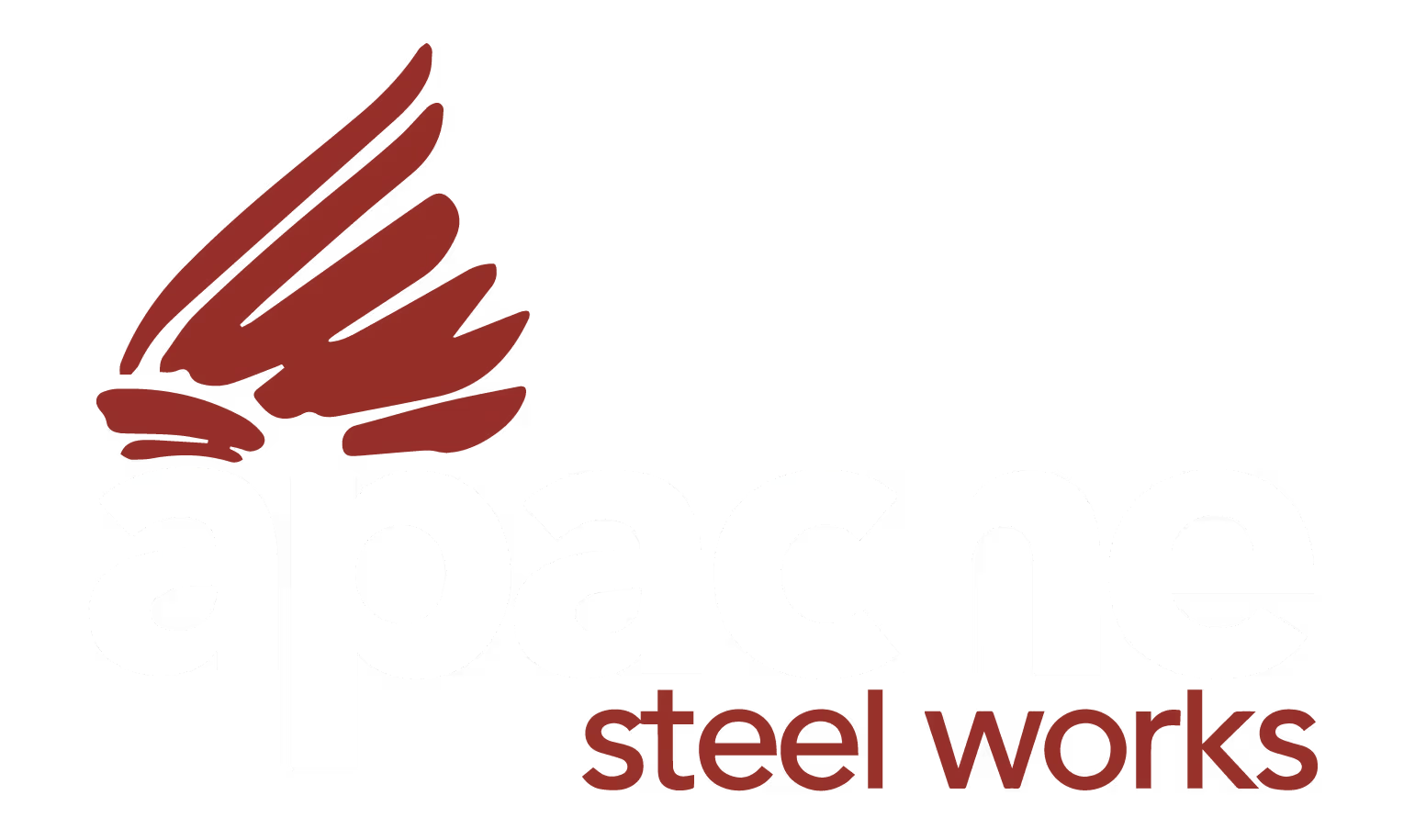
Plate Processing Company
Oxi Fuel Cutting Process and Fuel Gases Used
Oxi Fuel Cutting Process and Fuel Gases Used
Metal cutting processes require precise techniques for achieving clean, accurate cuts. The oxi fuel cutting process stands out for its effectiveness in handling thick metal materials, particularly in specialized facilities like those providing oxi fuel cutting in Houston, where industrial demands necessitate reliable cutting solutions.
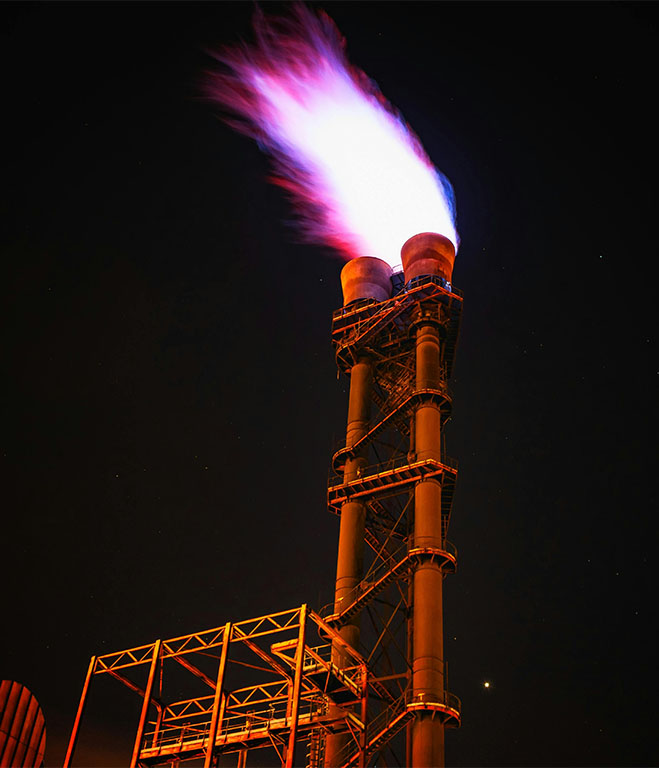
The Basic Principles Behind Oxi Fuel Cutting
The process begins with preheating the metal to its ignition temperature using a combination of oxygen and fuel gas. Many facilities offering oxi fuel cutting in Houston utilize this initial heating phase to prepare the metal surface for the main cutting action. The controlled preheating ensures consistent cut quality and prevents unwanted material deformation.
Common Fuel Gases and Their Properties
Different fuel gases produce varying flame temperatures and heating characteristics. Acetylene remains popular for its high flame temperature, while propane offers cost advantages. Professional oxi fuel cutting in Houston often employs multiple gas options to match specific project requirements and material thicknesses.
Maintaining proper temperature throughout the cutting process significantly impacts the final result. The interaction between oxygen and the heated metal creates a chemical reaction that facilitates the cutting action. This reaction must be carefully controlled to prevent excessive melting or irregular cuts.
The cutting torch assembly requires regular maintenance and careful adjustment. Facilities specializing in oxi fuel cutting in Houston maintain strict equipment standards to ensure consistent performance across different projects.
Material Thickness Considerations
Different metal thicknesses require specific cutting parameters. Thicker materials need higher oxygen pressures and adjusted cutting speeds. Understanding these relationships helps achieve optimal results across various material specifications and project requirements.
The quality of cut edges depends on several factors including cutting speed, oxygen pressure, and torch angle. Professional oxi fuel cutting in Houston emphasizes proper technique to minimize the need for secondary finishing operations. This attention to detail results in cleaner cuts and reduced post-processing time.
Safety Importance When Performing Oxy Fuel Cutting
Safe operation requires strict adherence to established procedures. This includes proper gas handling, equipment inspection, and workspace ventilation. Understanding and following safety protocols protects both operators and equipment while ensuring consistent cutting quality.
Various factors can affect cut quality, including worn nozzles, incorrect gas pressures, or improper torch angles. Identifying and addressing these issues quickly helps maintain productivity and cut quality. Regular equipment checks and operator training help prevent common problems.
Proper ventilation and fume management systems protect operators and comply with environmental regulations. Modern cutting facilities implement appropriate control measures to manage emissions and maintain safe working conditions.
What to Know Before Initiating Oxy Fuel Cutting
Clean metal surfaces free from rust, paint, or other contaminants ensure better cut quality. Proper material preparation helps achieve consistent results and prevents potential cutting issues. This preparation phase proves especially important for precision cutting requirements.
Conclusion
Understanding the complexities of oxi fuel cutting helps achieve better results across various applications. Whether cutting thick structural steel or performing precise shape cutting, this process continues to provide effective solutions for metal cutting needs.