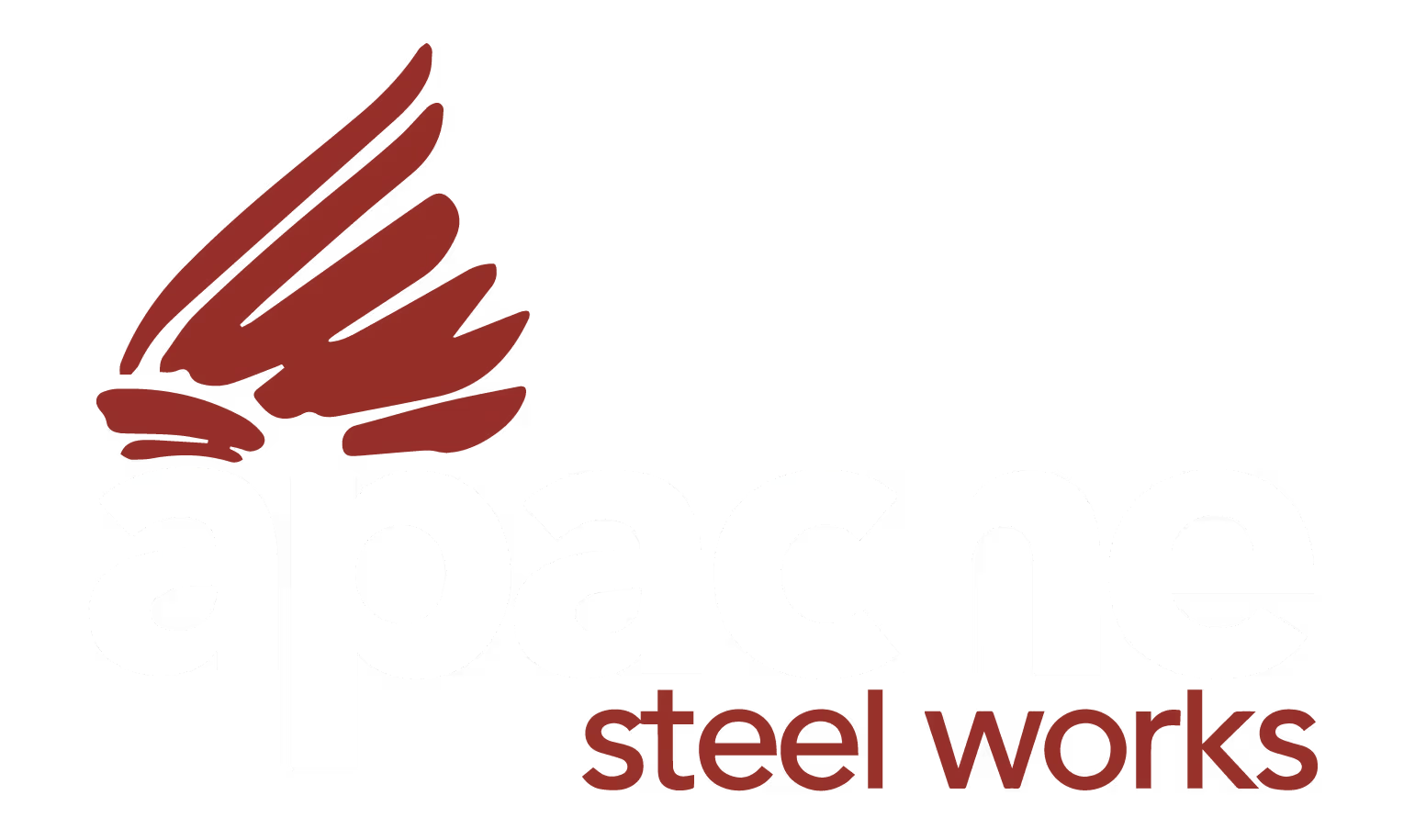
Plate Processing Company
Dealing with Common Oxy Fuel Cutting Problems
Dealing with Common Oxy Fuel Cutting Problems
Oxy fuel cutting is one of the most common processes used to cut ferrous metals using fuel gas and oxygen. While the oxy fuel process is one of the most efficient and productive metal cutting processes available, it can be plagued by various issues during operation.
Being aware of the different problems and solutions to them will assist in improving cut quality and safety in the workplace. So, let us look at some common issues during oxy fuel cutting in Houston and how they are remedied.
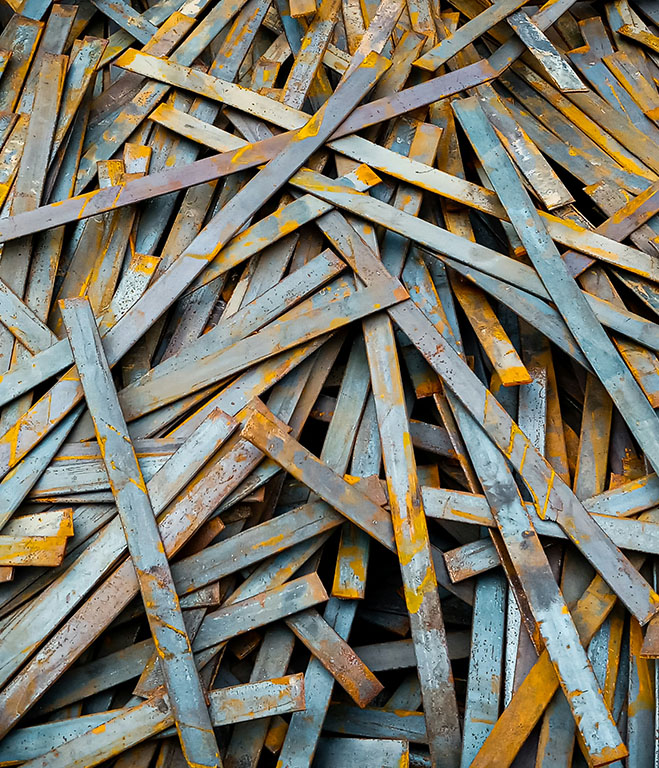
What Issues are Common During Oxy Fuel Cutting and How to Prevent Them
Poor Cut Quality
One of the most often seen problems during oxy fuel cutting is inconsistent or poor cut quality. This will be evident by noticing rough edges, excessive slag, or an inconsistent kerf. Poor cut quality can be a result of too slow or too fast cutting speed, incorrect gas pressures or the torch may be misaligned.
In this case, operators will want to ensure that the torch is at the correct angle and height while cutting. The operator should utilize the oxygen and fuel gas flow rates based on the thickness of the material being cut to ensure a smooth, clean cut.
Problems with Piercing of Material
Piercing thick materials can be one of the more difficult aspects of oxy fuel cutting. A common mistake is starting the cut without sufficient preheat. This will cause the pierce to not completely lip and will be troublesome until the material itself is cut.
Using a flame acceptable for the thickness of the metal along with enough time for the material to reach an ignition temperature will allow the operator to pierce.
Excessive Slag
Excessive slag is unwanted as well as indications of poor cutting parameters in oxy fuel cutting. Excessive slag can stem from having the torch too close or too far from the surface, or from an erratic travel speed, or from an inconsistent preheat flame.
In general, the torch would be held intricately at a right angle to the cutting surface and the cutting speed would be adjusted in order to maintain a consistent molten stream of metal that is moving downward.
Instability Induced Flashback
Flashbacks occur when the liquid and gases that travel through the hoses erupt into the shell or combustion chamber end of the torch arm itself. Flashbacks and backfires generally are caused by gas escape; too clogged tips; or improper pressure. To help avoid flashbacks and backfires a flashback arrestor should be placed at the torch.
Clean the cutting tips regularly. Perform proper shutdown procedures when stopping use to avoid sudden pressure drops which could induce backfires.
Torch Tip Erosion
Torch tip erosion is a consistent problem when cutting with oxy fuel torch nozzles. Torch erosion can develop when an operator runs their torch too long. Eroded tips change the gas flow pattern and lower the accuracy of the cut.
Erosion of the tip is usually caused by overheating, wrong gas mixtures, or the wrong tip size for the material thickness. Inspect tips regularly and replace worn tips. Operators should also check for the correct tip for the application and verify that gas pressures are set to manufacturer specifications.
Contact Apache Steel Works if you want an oxy fuel cutting service in Houston that can prevent such issues from arising in your projects.